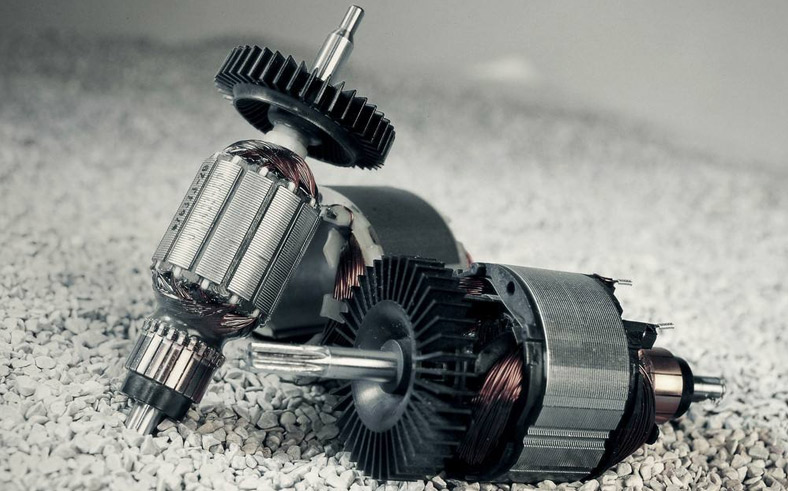
Rare earth permanent magnet motor is highly efficient and energy saving, the average power saving rate is as high as 10%, some special motor power saving rate is as high as 15% ~ 20%, and the price is reasonable. The high efficiency and energy saving rare earth permanent magnet motor developed in Our country, in terms of energy index and price, the foreign high-efficiency motor cannot be compared with it and has strong competitiveness in the international market. In 1992, former President Bush of the United States signed and approved the Energy Policy Act. According to this act, most of the general efficiency motors in the United States will no longer be produced, and only high-efficiency motors are allowed to be produced. After October 2002, the motors will be produced with higher efficiency, and after October 2007, the motors will reach the technical limit and the highest efficiency that is economically feasible.
In terms of energy saving, the rare earth permanent magnet motor is an ideal motor with a promising market prospect. China produces 36 million kW of various motors every year, of which the small motors below 18.5kW account for about 50%, and rare earth permanent magnet efficient and energy-saving motors have the most remarkable energy-saving effect in the type Motors. Rare earth permanent magnet motor in information industry, mechanical and electrical integration, automobiles, motorcycles, metallurgical equipment, fan, water pump, oil field equipment, textile machinery, household electrical appliances, and other fields has a broad application, including the starting rare permanent magnet is high efficiency and energy-saving motor oil field pumping unit gradually popularized, fan, water pump, and has set up a series product formation.
China's motor ownership is more than 400 million kW, annual consumption of 36 million kW, accounting for 60% of the total electricity consumption. In the fan, water pump matching motor accounted for 55% of the total, the annual consumption of electricity accounted for 40% of the total generation, and the current fan, water pump energy utilization is very low. According to the statistics of the National Bureau of Statistics in 1989, China has more than 37 million kinds of pumps and fans, with a supporting installed capacity of 1.1×105MW. The actual operation efficiency is less than 50%, the system operation efficiency is less than 30%, and the annual waste of electricity is about 20 billion kW·h. According to the power sector estimates, the coal industry fan, water pump, 50, 60's old. Equipment accounts for about 1/3, its operation efficiency is only 30% ~ 40%, the system operation efficiency is about 20%, for example, the consumption of large 5kW pump, often with 7.5KW motor, but often under 3kW load operation, measured efficiency is only 38%, resulting in huge energy waste, if the motor uses rare earth permanent magnet special motor, The cost of the motor only increases by 30% ~ 50%, and the operation efficiency can be improved to 50% ~ 55%, which fundamentally changes the situation of energy waste. If the annual production of 3 million kW rare earth permanent magnet motor can save 600 million yuan of power investment and 300 million yuan of electricity cost for the country.
Development of rare earth permanent magnet motor, in terms of reduced to import less and export more, also has the very vital significance, such as China's annual production of 10 million computers, for its disk drives all, rely on imports, or buy parts assembled in China, once the us-led western countries to our country import limit disk drives, China's computer production will be seriously affected. CNC machine tools, for example, cost more than $2.2 billion a year to import because of substandard motors and transmission control systems.
In terms of export trade, the significance is more prominent. As is known to all, every mechanical product should be equipped with an electric motor. American 1997, in the form of legislation to stop production general efficiency of the motor (with mass production in our country of Y series motor performance quite), Canada, Britain, Japan is also according to the United States to stop production general efficiency of the motor, if you don't take measures to speed up the development of energy-saving motor, we will soon lose machinery products in the international market. The price and performance of rare earth permanent magnet motor developed in China are very competitive in the international market, and some products have been exported.
Throughout the development of rare earth permanent magnet motors, the world's first motor that appeared in 1821 was permanent magnet motors. However, the magnetic energy product of permanent magnets used at that time was very low, and the motor made of huge volume and small capacity was soon replaced by electric excited motors. Until the 1960s, there has been the appearance of the diamond and NdFeB rare earth permanent magnet materials, with high remanence, high coercivity, and high magnetic energy product excellent performance, made into the motor with high efficiency and energy saving superior performance. As early as 1978, The French CEM company made an efficient and energy-saving motor of less than 18.5kW, but it was not popularized because of the high cost of using samarium cobalt permanent magnet.
Before 1983, due to the high cost of rare earth permanent magnets, research and development focused on aerospace and aerospace motors and high-tech fields requiring high performance without price being a major factor. The typical foreign products are 150kVAl2000 ~ 21000rpm rare earth cobalt permanent magnet starter/generator manufactured by GENERAL Electric Company in the United States. In China, 3kW2000rpm earth permanent magnet motor developed by the Shenyang University of Technology and 60 ~ 75kVA(later expanded to 160kVA) sparse cobalt permanent magnet auxiliary exciter and NdFeB auxiliary exciter jointly developed by Shenyang University of Technology, Dongdong Motor Factory, and Harbin Motor Factory.
In 1983, after the advent of NdFeB permanent magnet with higher magnetic properties and lower prices, the focus of domestic and foreign research and development shifted to industrial and civil electric machines. Foreign mainly is the computer hard disk drive motor, namely drives the read and write the magnetic head reciprocating motion of the linear motor one voice coil motor (VCM), CNC machine tools and robot brushless dc motor and luxury car starter motor. In China, there are various efficient permanent magnet synchronous motors, especially 0.8kW textile permanent magnet synchronous motors developed by Northwestern Polytechnical University.
In recent years, with the constant improvement of the rare earth permanent magnet material performance, especially the thermal stability of the NdFeB permanent magnet materials, the improvement of the corrosion resistance and gradually reduce the price and the further development of power electronics technology, the development of rare earth permanent magnet motor and should be entered a new stage, on the one hand, the results of original development in such aspects as national defense, industry and agriculture and daily life widely used; On the other hand, it is developing in the direction of high power (high speed, high torque), high function and miniaturization, expanding new electric varieties and application fields. At present, the capacity of a single rare-earth permanent magnet motor has exceeded 1000kW, the maximum speed has exceeded 300000rpm, the low speed is less than 0.01rplh, the minimum motor diameter is only 0.8mm, 1.2mm long. After the addition of NdFeB, permanent magnet excitation to the special motors such as stepping motors switched reluctance motors, and speed synchronous motors, the technical and economic performance, and dynamic response characteristics have been improved significantly.
The application of rare earth permanent magnet materials in motors is different in different countries. Japan's application in VCM accounts for about 50% of the total application of rare earth permanent magnet, the United States has a large application in the fields of aviation, aerospace, military, automobile and machine tools, etc., and Europe has the largest application in CNC machine tools. However, the total usage of rare earth magnetic steel in various motors is not much different from that of the total output of rare earth permanent magnets, generally 60% ~ 80%.
China is rich in rare earth resources, and the output of rare earth permanent magnet ranks first in the world. But two-thirds of rare-earth permanent-magnet material production is exported, and only a small percentage of domestic sales is used for motors. In the future, high efficiency and high-performance permanent magnet motors should be the focus of development, and quickly achieve industrialization.